1.4 FMEA概述
发布时间:2024年01月01日
FMEA适用场景
FMEA在三种基本情形下使用,每种情形都有不同的范围或重点。
情形1:新设计、新技术或新过程
情形2:现有设计或过程的新应用
- FMEA的范围包含新环境、新场地、新应用或使用概况(包括工作周期、法规要求等)下的现有设计或过程。FMEA的范围应当关注于新环境、新场地或新应用对现有设计或过程的影响。
情形3:对现有设计或过程的工程变更
- 新技术开发、新要求、产品召回和使用现场失效可能会需要变更设计和/或过程。在这种情况下,可能需要对FMEA进行审查或修订。
FMEA迭代场景
FMEA包含一系列关于设计或过程的知识,如果至少有以下一点适用,则可在生产开始后进行修改:
- 设计或过程的变更
- 操作条件变更
- 要求变更(法律、规范、顾客、或最新技术变更)
- 质量问题,即工厂经验、零公里、使用现场问题,内部/外部投诉
- 危害分析和风险评估(HARA)变更
- 威胁分析和风险评估(TARA)变更
- 产品监视过程中发现问题
- 经验教训
FMEA实施方法
FMEA主要有两种实施方法:根据产品功能(设计FMEA)或根据过程步骤(过程FMEA)进行分析。
1.4.1 设计FMEA (DFMEA)
- 概述: 设计FMEA(DFMEA)是一种主要由设计责任工程师/团队使用的分析技术,用于确保在将零件交付生产之前,尽可能考虑并解决在潜在失效模式及其相关失效起因或机理。
- 分析:?设计FMEA用于分析如块/边界图所示边界中所定义的系统、子系统或相关组件的功能,其内部要素之间的关系以及与系统边界外要素之间的关系。从而识别出可能存在的设计缺陷,将潜在的失效风险降到最低。
- 系统要素
1.4.2 过程FMEA (PFMEA)
- 概述: 设计FMEA(DFMEA)用于分析产品设计阶段可能产生的失效,过程FMEA(PFMEA)则与之不同,它分析的是制造、装配和物流过程中的潜在失效,以确保生产的产品符合设计目的。
- 分析: 过程FMEA通过考虑过程变差可能导致的潜在失效模式来分析过程,以确定预防措施的优先顺序,并根据需要改进控制。其总体目标是在生产开始之前分析过程并采取措施,以避免与制造和装配有关的不必要缺陷以及这些缺陷产生的后果。
1.4.3 不同FMEA之间的协作
- 协作概述: 在同一公司内部和公司外部,设计FMEA和过程FMEA都有协作的机会。为了有助于沟通影响和严重度,可以在各层级供应商之间对一个共同参与且达成一致的严重度评估进行评审。
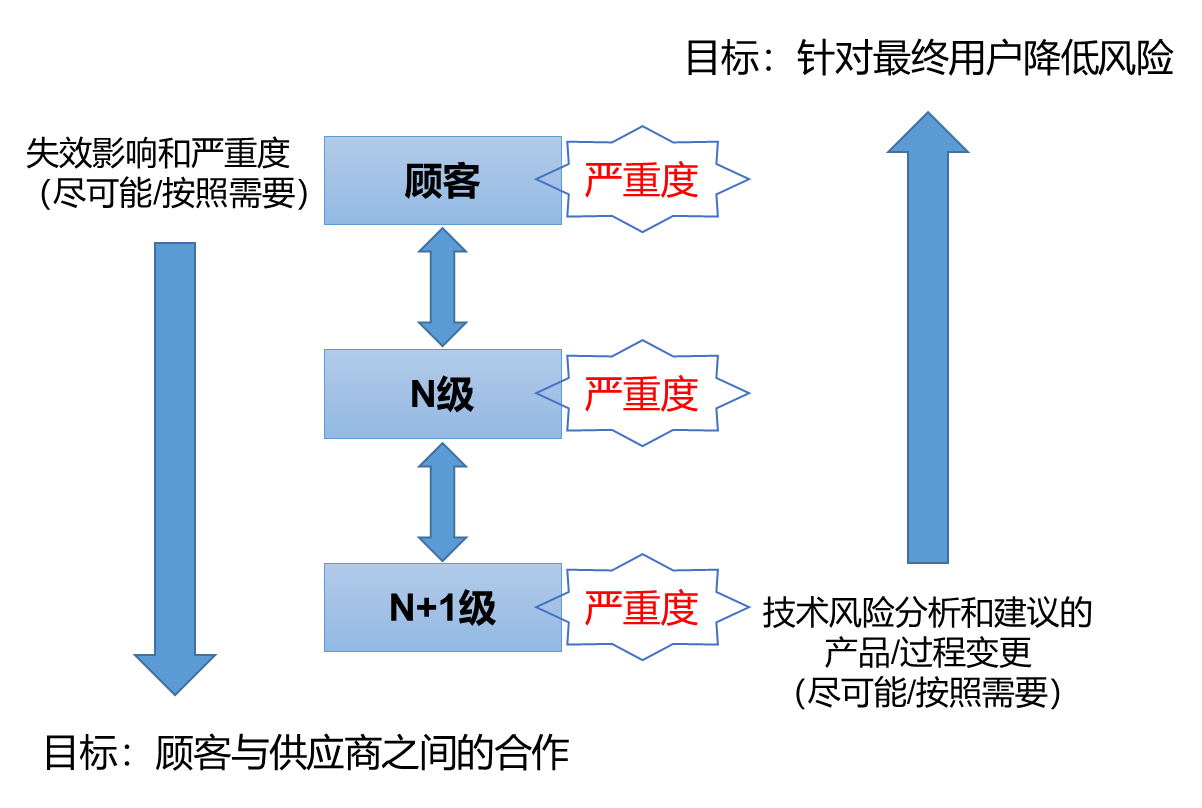
- 制造商策略: 对于制造商而言,一个好的开始是确保当失效影响相同时,设计FMEA和过程FMEA中的严重度也相同。需要建立一种相关性,以便使特定失效影响的设计中的失效特征也能在过程FMEA中捕获到相同特征(产品特性)的失效。
文章来源:https://blog.csdn.net/ChatCoding/article/details/135324674
本文来自互联网用户投稿,该文观点仅代表作者本人,不代表本站立场。本站仅提供信息存储空间服务,不拥有所有权,不承担相关法律责任。
如若内容造成侵权/违法违规/事实不符,请联系我的编程经验分享网邮箱:chenni525@qq.com进行投诉反馈,一经查实,立即删除!